This article introduces in detail the process of a gravel production line with an output of 300-500 cubic meters per hour, as well as the crushing equipment configuration plan and process design used. Shanghai Hengyuan has been committed to providing customers with valuable complete sets of crushed stone production line Solution, I hope this article can have reference and help for everyone.
1. Types of gravel
Note: Limestone is a material with low hardness. In this sandstone production line configuration proposal, impact crusher and fine crusher can be used as the fine crushing equipment in the second broken section.
The above equipment configuration does not include auxiliary parts such as belt conveyors, steel structures, concrete foundations, cables and wires; all equipment implements the national "three guarantees" policy, and the warranty period is one year (except for wearing parts); the payment method and issuance of equipment Please consult our sales staff for the delivery cycle.
3. Process flow of sand and gravel production line
1. Equipment selection of head-breaking unit
The model of the vibrating feeder is ZSW600 * 130 feeder, which provides uniform feeding for the gravel production line.
The sieving function of the vibrating feeder can ensure that the soil impurities and crushed materials in the stone are separated out, and then finely sieved by the combined YK1860 vibrating screen to separate out the mixed soil waste less than 20mm, thus ensuring the stone Quality, and achieve the minimum loss of raw materials. The jaw crusher adopts PE1000 * 1200 model, which can meet the crushing requirement of the maximum feeding particle size of 850mm. The large material sieved by the vibrating feeder and the small material recovered by the desilting screen enter the jaw crusher for crushing.
Picture: Vibrating feeder, jaw crusher (combined installation diagram)
Picture: Vibration feeder and jaw crusher site picture
The large feed silo is designed in front of the vibrating feeder to meet the continuous high-flow feeding requirements of the production line; the loading truck can directly discharge the large hopper, or the loader can directly load the feed to the feeder.
2. Equipment selection of the second-breaking unit
Adopt impact crusher, model: PF1515, to provide secondary crushing for gravel production line.
Process description:
After the treatment of the head breaking system, the particle size of the stone is reduced to less than 250mm, of which more than 80% is reduced to less than 200mm. Then, it is transported to the intermediate silo for buffering through a belt conveyor with a width of 1.4 meters.
The intermediate silo has a buffer capacity of a certain amount of storage. When the feed volume of the head breaking system is not sufficient, it can meet the feeding amount of the second breaking system for several hours, thereby avoiding the no-load phenomenon of the second breaking and subsequent systems, and thus achieving production benefits Maximization.
The buffer material in the intermediate silo is evenly conveyed to two large-scale PF1515 impact crushers in parallel through the model GZG-1253 hanging feeder at the bottom of the silo to complete the second stage crushing operation. The impact crusher PF1515 has strong crushing ability, can crush the stone particle size to the centimeter level specification, and has a certain granularity.
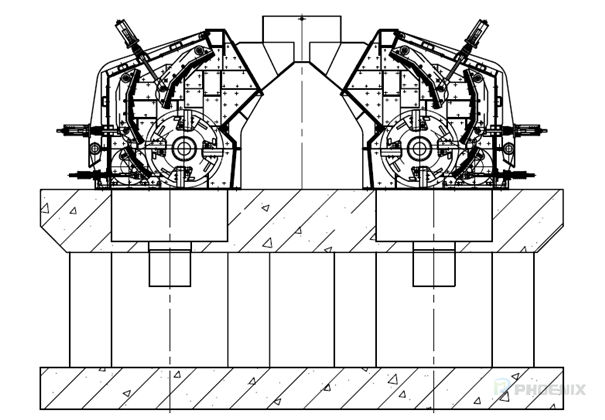
Picture: Impact crusher (installation sketch)
Picture: Impact crusher site
Two large-scale counterattacks in parallel share a reverse belt conveyor under the equipment, and the two counterattacked discharges are transported in parallel, lapped to the subsequent main belt conveyor with a width of 1.4 meters, and sent to the next level of vibrating screen Sieving.
3. Selection of one screening unit
The vibrating screen is adopted, the model is YK series, and the recommended model is 3YK3072 vibrating screen, which provides material screening for the gravel production line.
Process description:
After two stages of crushing, the particle size of the stone is basically reduced to the centimeter level. Our production line adopts two large-scale 3YK3072 circular vibrating screens connected in parallel to screen the centimeter-level mixture for one time.
Figure: Vibrating screen (installation sketch)
Figure: Vibrating screen scene
Process description:
The four discharges of 3YK3072 vibrating screen enter different follow-up operation processes.
a. 0-6mm, directly used as finished product, and transported to the subsequent screening equipment to complete 0-3mm, 3-6mm screening pile;
b. 6-11mm, vibrating screen adopts two-way outlet design:
Figure: Sketch of the two-way discharge port
A direction to the discharge port, 6-11mm material is used as the finished material, and it is transported to the subsequent screening equipment, and the material is piled after screening;
B to the discharge port, 6-11mm material is sent to the fine crusher for sand making. Choose different outlets to achieve different running tasks;
c. 11-31.5mm, as semi-finished material, transported to model HB1000 sand making and shaping machine for shaping and crushing, so as to obtain stone aggregate with excellent grain shape;
d. If it is greater than 31.5mm, it will be transported to the fine crusher for the third-level crushing operation.
4. Selection of ultra-high fine crushing unit
Adopt high-efficiency fine crusher, model is PCD1616, which can provide finer crushing process for sand and gravel production line.
Process description:
Two large-scale PCD1616 ultra-high fine crushers are used to achieve high-efficiency refinement and crushing tasks. High-efficiency fine crusher adopts advanced split hammer breaking structure and high-frequency counterattack forced crushing technology, which can obtain the highest efficiency fine crushing effect. Therefore, the fine crushing unit can not only completely refine the 6-11mm intermediate material with little demand into machine sand less than 6mm, but also completely digest the return material larger than 31mm.
The high-efficiency fine crusher PCD1616 adopts a split high-chromium alloy material hammer head, which has super wear resistance and outstanding performance in the application of limestone crushing production lines. .
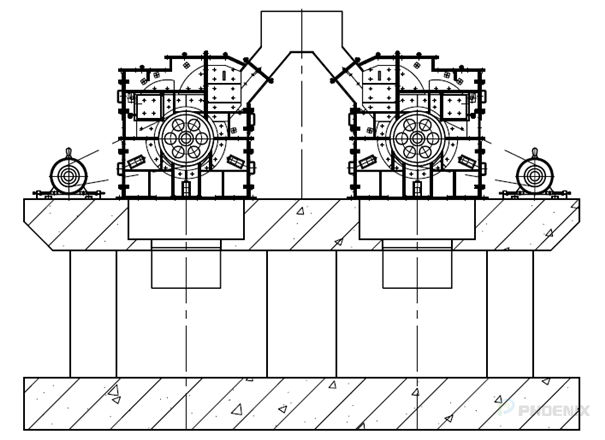
Figure: High-efficiency fine crusher (simplified installation combination)
Figure: Fine crusher site
Two parallel PCD1616 high-efficiency fine crushers share a pour belt conveyor under the equipment, and parallelly transport the two counter-crushed discharges to the subsequent 1.4-meter-wide main belt conveyor to the next level of vibrating screen Sieving. Two parallel PCD1616 high-efficiency fine crushers and two PF1515 large-scale impact breakers share a main belt conveyor, thus achieving a simplified layout effect and reducing intermediate energy consumption and space occupation.
5. Selection of the whole unit
Adopt sand making and shaping machine, model is HB1000 series, to provide finished products with excellent grain shape for sand and gravel production line.
Technological process description: The stone material passes through the bipolar crushing operation of jaw crushing and counterattack crushing, and a single screening unit, after screening 11-31.5mm semi-finished products, it is conveyed to the complete unit through a belt conveyor. The production line process design uses two HB1000 shaping machines in parallel operation. All the 11-31.5mm semi-finished materials sieved at one time are completely crushed, so as to obtain finished stone aggregates with excellent grain shape.
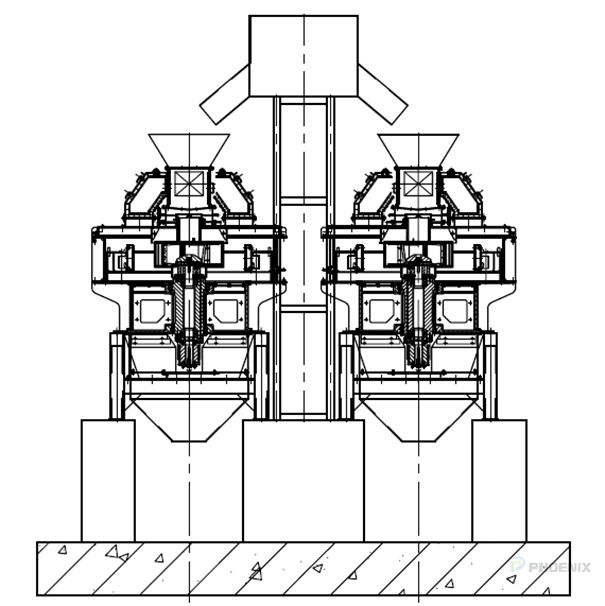
Figure: Sand Making and Shaping Machine (Simple Installation Drawing)
Figure: Site map of sand making machine
HB series shaping machine adopts high-speed, centrifugal, impact shaping technology, which can optimize the granule shape of stone to the greatest extent, so as to meet the technical requirements of various high-grade stone aggregates. Two parallel HB1000 high-speed shapers share a pour belt conveyor under the equipment, and the discharge of the two shaping machines are conveyed in parallel, and then connected to the subsequent 1.2-meter-wide belt conveyor to the next level of vibrating screen Sieving.
6. Selection of finished material screening unit
There are 6 kinds of finished materials in this sand and gravel production line, as shown in the following table:
Finished product type |
0~3mm |
3~6mm |
6~11mm |
11~19mm |
19~26.5mm |
26.5~31.5mm |
Scale range |
30% |
20% |
5% |
20% |
10% |
10% |
Process description:
According to the process design of our limestone sandstone production line, the materials in the range of 0-19mm account for 80% of the finished product, and the screening operations are completed by two large 3YK3072 circular vibrating screens; the materials in the range of 19-31.5mm account for 20% of the finished product, and one 3YK3072 large circular vibrating screen completes the screening operation. The finished product screening unit and primary screening unit adopt the same specification model 3YK3072, which can realize the complete interchange and universal use of spare parts, thereby reducing the spare parts inventory, reducing the backlog of spare parts, and improving the convenience of maintenance and maintenance of the vibrating screen. .
7. Type selection of desilting screen equipment
The application of the soil removal screen can ensure that the soil impurities in the raw materials are completely removed, so as to obtain high-quality gravel aggregates.
Process description:
The sieving function of the vibrating feeder can only achieve partial sieving, and cannot completely sieve the soil impurities in the raw materials. If complete soil removal cannot be achieved, high-quality aggregates cannot be obtained. Therefore, our company uses a separate parallel YK1860 vibrating screen as a soil removal screen. The design purpose is very clear, that is, to remove the soil impurities in the raw materials and obtain high-quality finished materials. In addition, the use of a separate earth removal screen can recover useful stones from the waste and reduce the raw material loss rate. During the long-term operation, the amount recovered will be considerable and the economic benefits will be significant.
8. Others:
Based on the design concept of high efficiency, energy saving, stability and reliability, based on many years of practical experience, our company designs and completes the technological process of this production line and continuously upgrades and optimizes it. Readers and experts are invited to criticize and correct, so as to integrate the experience and technology of all parties to obtain better design and operation results. Thank you very much for reading this article!
This article was originally published by Shanghai Hengyuan Metallurgical Equipment Co., Ltd. www.shhyyj.com, if you need to purchase equipment, please send an email to info@shhyyj.com, and reply to you immediately after receiving it.